With Teknologi Digital Tantang Metode Manufaktur Tradisional, the traditional manufacturing landscape is undergoing a significant transformation. Rapid advancements in digital technologies, from automation to AI, are disrupting established processes and creating new opportunities for innovation. This shift presents both challenges and exciting possibilities for businesses seeking to remain competitive in the modern market.
The current state of traditional manufacturing, often characterized by limitations in efficiency and flexibility, is contrasted with the potential offered by digital technologies. This analysis explores the challenges and benefits of integrating digital solutions into traditional manufacturing processes, highlighting key technologies, successful case studies, and the future outlook for the industry.
Introduction to Digital Technology’s Impact on Traditional Manufacturing
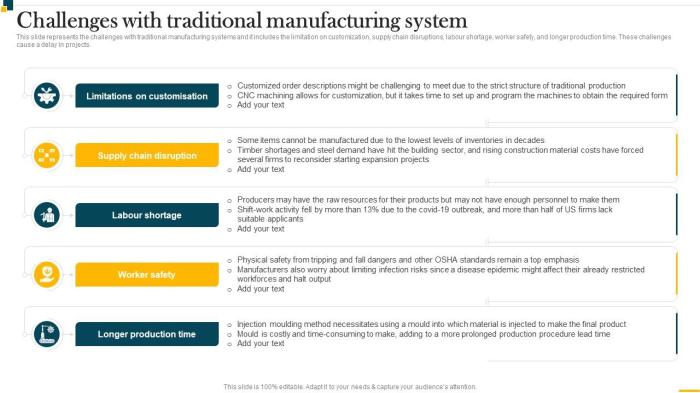
Source: slideteam.net
Traditional manufacturing methods, often relying on manual labor and standardized processes, have been the backbone of industrial production for decades. However, these methods face challenges in terms of efficiency, flexibility, and adaptability to changing market demands. The limitations of traditional manufacturing processes, such as high production costs and low customization capabilities, are increasingly being challenged by the rapid advancements in digital technologies.The digital revolution is reshaping various industries, driving innovation and efficiency gains.
This transformation is particularly pronounced in the manufacturing sector, where digital technologies are automating tasks, optimizing workflows, and enabling unprecedented levels of customization. The convergence of digital technologies with manufacturing practices is poised to revolutionize how products are designed, produced, and delivered.
Current State of Traditional Manufacturing Methods
Traditional manufacturing methods typically involve linear, sequential processes, often relying on manual labor and standardized procedures. This approach can be inflexible, inefficient, and costly to adapt to changes in demand or product specifications. The lack of real-time data and feedback loops hinders process optimization and leads to potential inefficiencies. Moreover, traditional methods often struggle with complex product designs and intricate manufacturing processes.
Rapid Advancement of Digital Technologies
Digital technologies are advancing at an unprecedented pace, with innovations in areas such as artificial intelligence (AI), machine learning (ML), the Internet of Things (IoT), and 3D printing. These technologies are being integrated into various industries, creating opportunities for automation, data-driven decision-making, and enhanced product design. The rise of cloud computing and big data analytics allows for real-time monitoring and analysis of manufacturing processes, leading to improved productivity and reduced waste.
Disruptive Impact of Digital Technology
Digital technologies have the potential to disrupt traditional manufacturing practices by automating complex tasks, optimizing workflows, and improving product design and customization. The ability to collect and analyze vast amounts of data in real-time allows for more accurate predictions, proactive maintenance, and faster response times to changing market conditions. Furthermore, digital technologies facilitate greater flexibility and customization, enabling manufacturers to cater to niche markets and individual customer needs.
Key Characteristics of Digital Technologies Relevant to Manufacturing
Digital technologies relevant to manufacturing are characterized by their ability to automate processes, collect and analyze data, and enhance communication and collaboration. The integration of these technologies enables real-time monitoring, predictive maintenance, and enhanced decision-making. Moreover, digital technologies facilitate a more flexible and adaptable manufacturing environment, enabling customization and rapid response to market demands. Crucially, they enable greater transparency and traceability throughout the manufacturing process.
Examples of Digital Technologies in Manufacturing Processes
Digital technologies are already being implemented in various manufacturing processes, driving efficiency and innovation. For example, robotic process automation (RPA) is used to automate repetitive tasks, leading to reduced labor costs and increased production speed. The use of machine learning algorithms allows for predictive maintenance, reducing downtime and improving equipment lifespan. Moreover, 3D printing is enabling the creation of complex and customized products, while the IoT facilitates real-time monitoring and control of manufacturing equipment.
These examples highlight the significant impact digital technologies are having on the manufacturing landscape.
Examining Specific Challenges Faced by Traditional Manufacturing
Traditional manufacturing methods, while often deeply ingrained in a company’s history and processes, frequently encounter significant limitations in the face of rapidly evolving technological advancements and market demands. These limitations hinder efficiency, impact profitability, and create difficulties in adapting to contemporary consumer preferences. Understanding these challenges is crucial for navigating the transition to more advanced manufacturing strategies.
Key Limitations of Traditional Manufacturing Methods
Traditional manufacturing methods, while often cost-effective in specific contexts, are often constrained by their rigid structures and lack of adaptability. This rigidity frequently translates into difficulties in responding quickly to market changes and evolving customer demands. Moreover, the reliance on manual labor and specialized equipment can limit the production volume and overall output.
Efficiency Challenges in Traditional Manufacturing
Traditional manufacturing often struggles with optimizing workflow and minimizing bottlenecks. Inefficient material handling systems, inconsistent work processes, and a lack of automation contribute to production delays and reduced overall efficiency. These inefficiencies translate into higher production costs and lower output compared to modern, digitally-driven alternatives. For example, a garment factory relying solely on manual cutting and sewing techniques may find its production rate significantly hampered compared to a factory incorporating automated cutting machines and robotic sewing arms.
Cost Considerations in Traditional Manufacturing
The costs associated with traditional manufacturing can be multifaceted. High labor costs, particularly in labor-intensive processes, can strain profitability. Moreover, the need for extensive capital investment in specialized equipment, particularly if such equipment is not easily adaptable, can contribute to substantial upfront expenses. The limited flexibility inherent in these methods can also lead to substantial costs associated with redesigning or modifying processes for new products or orders.
Furthermore, inventory management and storage can be costly, leading to significant warehousing needs and associated operational expenses.
Quality Challenges in Traditional Manufacturing
Maintaining consistent quality in traditional manufacturing can be a significant challenge. Variability in human labor and the inherent limitations of manual inspection methods can lead to inconsistent product quality. Without the use of advanced monitoring and quality control systems, identifying and rectifying defects can be a time-consuming and costly process. For instance, a furniture manufacturer relying on hand-finishing techniques may encounter variations in the final product finish quality, while a factory employing automated quality control checks can maintain a more consistent product quality standard.
Flexibility Challenges in Traditional Manufacturing
Adapting to fluctuating market demands and introducing new product lines presents significant challenges for traditional manufacturing setups. The rigidity of the processes and the reliance on specialized equipment often result in lengthy lead times for implementing changes in production. This inflexibility can limit the company’s ability to react swiftly to shifts in consumer preferences or sudden changes in market trends.
For example, a bakery that primarily bakes traditional bread types may find it difficult to rapidly introduce new product lines, such as gluten-free options, due to the limitations in their current equipment and production setup.
Adapting to Evolving Customer Demands and Market Trends
Traditional manufacturing often struggles to meet the growing demand for customization and personalization in products. The inflexibility of their methods can lead to difficulties in quickly adapting to evolving customer preferences and market trends. This lack of agility can result in lost sales opportunities and a diminished market share. For instance, a manufacturer of standard-sized furniture might face difficulties in meeting the growing demand for custom-sized furniture, as their current production lines are not equipped to handle such variations.
Role of Human Capital in Traditional Manufacturing
The human capital within traditional manufacturing settings plays a critical role in the success of the organization. Skilled labor and experienced artisans are essential for maintaining the quality and efficiency of the production process. However, the need for skilled workers can be a significant challenge in many settings, especially with the increasing difficulty of finding and retaining skilled labor.
Further, providing adequate training and development opportunities for the workforce can help to mitigate this challenge.
Specific Industries Facing Challenges
Traditional manufacturing challenges are not limited to any specific industry, but several sectors are particularly vulnerable to these constraints. Examples include:
- The automotive industry, where complex and customized parts are increasingly demanded, and traditional assembly lines can be challenging to modify.
- The textile industry, which faces increasing pressure to reduce production times and improve product quality, while maintaining cost-effectiveness.
- The food processing industry, where maintaining high standards of hygiene and food safety while meeting increasing consumer demands for diverse and customized products poses significant challenges.
Exploring the Potential Benefits of Digital Technologies
Digital technologies present a compelling opportunity for traditional manufacturing businesses to enhance their operations and gain a competitive edge. By embracing these advancements, manufacturers can achieve significant improvements in efficiency, productivity, and cost reduction, ultimately strengthening their position in the market. This section will detail the numerous advantages of integrating digital technologies into existing manufacturing processes.
Enhanced Efficiency and Productivity
The implementation of digital technologies can dramatically boost efficiency and productivity across the manufacturing spectrum. Sophisticated software and automated systems streamline workflows, reduce manual intervention, and minimize errors, thereby accelerating production cycles. Real-time data analytics provide insights into operational bottlenecks, enabling proactive adjustments and optimized resource allocation.
- Automated Material Handling and Logistics: Automated guided vehicles (AGVs) and robotic systems can transport materials and components with precision and speed, eliminating delays and improving overall logistics. This not only increases productivity but also minimizes human error in handling tasks.
- Predictive Maintenance: Digital sensors and data analytics allow manufacturers to predict equipment failures before they occur. This proactive approach prevents costly downtime and maximizes equipment lifespan. Predictive maintenance can significantly reduce maintenance costs and increase uptime.
- Optimized Production Schedules: Advanced scheduling software enables manufacturers to optimize production schedules based on real-time demand and resource availability. This reduces inventory costs and ensures that production meets customer demands efficiently.
Improved Quality Control
Digital technologies facilitate robust quality control mechanisms throughout the manufacturing process. Advanced sensors, imaging systems, and data analytics allow for continuous monitoring and evaluation of product quality, enabling the detection of defects and inconsistencies early in the process.
- Real-Time Quality Inspection: Computer vision systems and machine learning algorithms can inspect products in real-time, identifying defects with high accuracy. This allows for immediate corrective action and prevents faulty products from entering the supply chain.
- Statistical Process Control (SPC): Digital tools enable manufacturers to implement SPC techniques, monitoring key process parameters and detecting deviations from acceptable standards. This proactive approach to quality control minimizes waste and enhances product consistency.
Streamlined Product Development
Digital technologies significantly accelerate product development cycles. Computer-aided design (CAD) and computer-aided manufacturing (CAM) software facilitate rapid prototyping and design iterations. Virtual simulations allow for testing and optimization of product performance before physical prototypes are created.
- Rapid Prototyping: 3D printing and other rapid prototyping technologies enable the creation of physical prototypes quickly and efficiently. This accelerates the design process and allows for faster iterations and adjustments based on feedback.
- Virtual Design and Simulation: Virtual design and simulation tools allow manufacturers to test and optimize product performance in a virtual environment, reducing the need for costly physical testing and improving design efficiency.
Enhanced Flexibility and Adaptability
Digital technologies empower traditional manufacturing businesses to adapt more swiftly to changing market demands. Modular designs, flexible manufacturing systems, and real-time data analytics facilitate the adjustment of production processes to accommodate fluctuating orders and new product requirements.
- Customization and Mass Customization: Digital technologies allow manufacturers to tailor products to specific customer needs more easily, enabling mass customization and satisfying diverse demands. This is achieved through modular design and automated adjustments to production lines.
- Agile Manufacturing: Real-time data and flexible production systems enable a more agile approach to manufacturing. Responding to changes in customer orders or market trends becomes quicker and more efficient, leading to faster turnaround times.
Examples of Digital Technologies
Several digital technologies offer significant benefits to traditional manufacturing. These include:
- 3D Printing: Rapid prototyping and customized production are key benefits.
- Industrial Internet of Things (IIoT): Real-time data collection and analysis enable predictive maintenance and improved process optimization.
- Computer-Aided Design (CAD) and Computer-Aided Manufacturing (CAM): Improved design efficiency and automated manufacturing processes are facilitated.
Specific Digital Technologies and Their Impact on Traditional Manufacturing
Digital technologies are rapidly reshaping traditional manufacturing landscapes, introducing new efficiencies and possibilities. This transformation is driven by automation, machine learning, data analytics, and additive manufacturing, all impacting how products are designed, produced, and ultimately, delivered. The integration of these technologies allows for enhanced precision, reduced waste, and increased adaptability in the manufacturing process.
Automation’s Influence on Traditional Manufacturing Methods
Automation significantly alters traditional manufacturing methods by streamlining workflows and reducing reliance on manual labor. This leads to increased output, improved consistency, and potentially lower production costs. Traditional methods often involve repetitive tasks, which are ideally suited for automation.
- Enhanced Efficiency and Productivity: Automated systems can operate continuously, 24/7, maximizing production output. This contrasts with human limitations and the need for breaks, leading to increased efficiency and productivity gains. For instance, robotic arms in assembly lines can perform tasks with precision and speed surpassing human capabilities.
- Improved Quality and Consistency: Automation tools often eliminate human error, resulting in improved product quality and consistent output. Precision machining, for example, is highly dependent on automation for maintaining tight tolerances and accuracy in producing components.
- Reduced Labor Costs: While initial investment in automation can be substantial, long-term cost savings are often realized through reduced labor expenses and increased output.
Examples of Automation Transforming Manufacturing Workflows
Automation tools are transforming manufacturing workflows across various industries. Consider automated guided vehicles (AGVs) in warehousing and logistics, or robots in assembly lines. These examples highlight how automation enhances speed and precision in handling materials and assembling products.
- Automated Material Handling Systems: AGVs and conveyor systems automate the movement of materials, enabling faster and more efficient logistics within the manufacturing facility.
- Robotic Process Automation (RPA): RPA automates repetitive administrative tasks, such as data entry and order processing, freeing up human workers for more strategic roles.
- CNC Machining: Computer Numerical Control (CNC) machines automate complex machining tasks, allowing for high precision and customization in producing components.
Impact of Machine Learning and AI on Manufacturing Decision-Making
Machine learning (ML) and artificial intelligence (AI) are enhancing manufacturing decision-making by enabling predictive maintenance, optimizing production schedules, and improving quality control. The ability to analyze vast datasets allows for more informed and proactive decision-making, reducing downtime and increasing overall efficiency.
- Predictive Maintenance: AI algorithms analyze sensor data from machines to predict potential failures, allowing for proactive maintenance and reducing unplanned downtime.
- Process Optimization: Machine learning models can identify bottlenecks and inefficiencies in production processes, leading to optimized workflows and reduced waste.
- Improved Quality Control: AI can be used to identify defects in products with greater accuracy and speed than traditional methods, enhancing product quality and reducing rejects.
The Role of Data Analytics in Optimizing Manufacturing Processes
Data analytics plays a critical role in optimizing manufacturing processes by providing insights into various aspects of production. This allows manufacturers to identify areas for improvement, track performance metrics, and make data-driven decisions.
- Real-time Monitoring: Real-time data analysis allows for continuous monitoring of production processes, enabling rapid response to issues and adjustments to improve efficiency.
- Performance Metrics Tracking: Data analytics helps track key performance indicators (KPIs), such as production output, quality rates, and resource utilization, allowing for targeted improvement strategies.
- Demand Forecasting: Data analytics helps predict future demand, enabling manufacturers to adjust production schedules and inventory levels accordingly.
How 3D Printing and Additive Manufacturing Techniques Can Disrupt Traditional Methods
D printing, or additive manufacturing, is disrupting traditional manufacturing by enabling the creation of complex geometries and customized parts with reduced material waste. This technology offers greater design flexibility and shorter production cycles, leading to faster time-to-market and potentially lower costs for prototyping and production.
- Customization and Design Flexibility: 3D printing allows for the creation of customized parts and designs that are difficult or impossible to achieve with traditional methods.
- Reduced Material Waste: Additive manufacturing uses only the required material, unlike subtractive manufacturing methods which often result in significant material waste.
- Faster Prototyping and Production Cycles: 3D printing significantly accelerates the prototyping and production process, enabling faster time-to-market for new products.
Comparison of Traditional and Digitally Enhanced Manufacturing Methods
Method | Advantages | Disadvantages | Digital Enhancement |
---|---|---|---|
Traditional Machining | Established processes, readily available tools | High material waste, longer lead times, limited design flexibility | CNC machining, CAD design, automation |
Injection Molding | High production volume, cost-effective for high-volume parts | High initial tooling costs, limited design complexity | Optimized tooling design, AI-driven process control |
Traditional Assembly | Simple assembly steps | Potential for human error, slower speed, lower efficiency | Robotic assembly, automated guided vehicles (AGVs) |
Case Studies of Successful Digital Transformations
Real-world examples demonstrate the tangible benefits of integrating digital technologies into manufacturing processes. These transformations often involve significant shifts in operations, necessitating careful planning and execution. Successful implementations frequently lead to enhanced efficiency, reduced costs, and improved product quality.Companies embracing digital transformation have shown that it’s not merely about adopting new technologies, but also about adapting existing workflows and cultivating a culture of innovation.
Strategic planning, employee training, and continuous improvement are crucial for reaping the full potential of digital tools.
Examples of Successful Digital Transformations
Several companies have successfully integrated digital technologies into their manufacturing processes, resulting in notable improvements. These implementations highlight the various approaches and outcomes achievable through such transformations.
- Siemens’ Digital Factory Initiative: Siemens, a global leader in industrial automation and engineering, has implemented a digital factory initiative across its manufacturing operations. This involved leveraging advanced software, data analytics, and automation technologies to optimize production processes. The outcome included significant improvements in efficiency, reduced downtime, and enhanced product quality. Key takeaways include the importance of a comprehensive approach that encompasses multiple digital technologies and the potential for substantial cost savings and improved operational performance.
- General Electric’s Predix Platform: General Electric (GE) utilizes the Predix platform to connect and analyze data from its industrial equipment. This allows for predictive maintenance, real-time monitoring, and improved operational efficiency across various industries. By implementing this digital platform, GE has optimized its supply chain, reduced maintenance costs, and improved overall equipment effectiveness.
- Toyota’s Lean Manufacturing with Digital Integration: Toyota, known for its lean manufacturing principles, has integrated digital technologies to enhance its efficiency. This includes using digital tools for process optimization, real-time data analysis, and collaborative work environments. The benefits of this integration include improved quality, reduced waste, and enhanced customer responsiveness. The key takeaway is the potential of integrating established methodologies with digital advancements to maximize efficiency and responsiveness.
Stages of Digital Transformation in Case Studies
A comparative analysis of these case studies reveals different stages of digital transformation. The following table Artikels the key aspects of these transformations.
Company | Stage | Technologies Used | Results |
---|---|---|---|
Siemens | Advanced Digital Factory | Advanced software, data analytics, automation | Improved efficiency, reduced downtime, enhanced product quality |
General Electric | Data-driven Optimization | Predix platform, real-time monitoring, predictive maintenance | Optimized supply chain, reduced maintenance costs, improved equipment effectiveness |
Toyota | Lean Manufacturing with Digital Integration | Digital tools for process optimization, real-time data analysis, collaborative work environments | Improved quality, reduced waste, enhanced customer responsiveness |
The Future of Manufacturing in the Digital Age
The digital revolution is reshaping the manufacturing landscape, driving significant transformations in processes, products, and the workforce. This shift promises enhanced efficiency, increased customization, and greater flexibility, but also presents new challenges and opportunities for companies and individuals alike. The future of manufacturing hinges on embracing these changes and adapting to the evolving demands of a digitally driven world.The long-term impact of digital technologies will be profound, extending beyond automating existing tasks to fundamentally altering the nature of production itself.
The integration of advanced technologies like artificial intelligence, machine learning, and the Internet of Things (IoT) will enable unprecedented levels of precision, agility, and responsiveness in manufacturing processes. This, in turn, will lead to higher quality products, reduced production costs, and shorter lead times.
Long-Term Impact of Digital Technologies
Digital technologies are poised to revolutionize manufacturing across the board. Automation will play a critical role, with robots and AI-powered systems taking on increasingly complex tasks, leading to greater efficiency and reduced human error. The Internet of Things will provide real-time data insights, allowing manufacturers to optimize processes and predict potential issues. This continuous monitoring and analysis will foster a more proactive and predictive approach to manufacturing.
Potential Shifts in Job Roles and Skills Requirements
The rise of automation will inevitably lead to shifts in job roles. Traditional manufacturing jobs requiring repetitive tasks may be replaced by roles focused on operating, maintaining, and managing advanced machinery. The demand for skilled technicians proficient in data analysis, programming, and digital technologies will increase. Upskilling and reskilling initiatives will be crucial for workers to adapt to these changes.
For example, companies like General Electric are already investing heavily in training programs to equip their workforce with the necessary skills for a digital future.
Role of Collaboration and Partnerships in the Digital Manufacturing Landscape, Teknologi Digital Tantang Metode Manufaktur Tradisional
Collaboration and partnerships will be essential for navigating the complexities of the digital manufacturing landscape. Sharing data, expertise, and resources through partnerships will enable manufacturers to access advanced technologies and expertise they may not have in-house. This collaboration can extend to the development of new products and processes, fostering innovation and growth.
Potential Challenges and Opportunities for the Industry
The digital transformation of manufacturing presents both challenges and opportunities. The initial investment in new technologies and the need for reskilling the workforce can be substantial hurdles. However, the potential for increased efficiency, reduced costs, and enhanced product quality offers significant advantages. For instance, companies using 3D printing are already realizing substantial cost savings and quicker product development cycles.
Emerging Trends in Digital Manufacturing and Their Implications
Several emerging trends in digital manufacturing are shaping the future of the industry. These include the growing adoption of additive manufacturing (3D printing), the use of augmented reality (AR) and virtual reality (VR) for training and design, and the increasing importance of data analytics for process optimization. These trends highlight the increasing integration of digital technologies across all aspects of manufacturing, leading to more flexible, agile, and efficient operations.
Strategies for Adapting Traditional Manufacturing to Digital Technologies
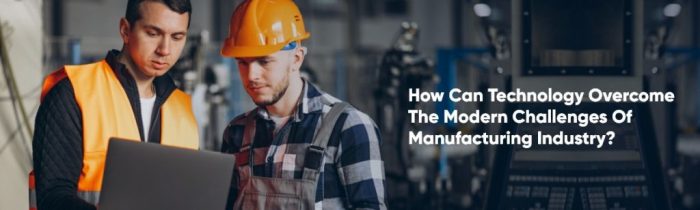
Source: clavax.com
A smooth transition to digital technologies is crucial for traditional manufacturing businesses to remain competitive in the modern market. This necessitates a well-defined strategy that accounts for the specific needs and resources of each organization. Ignoring the complexities of this transformation can lead to wasted resources and ultimately, a slower or failed adoption of these beneficial technologies.Successfully navigating this digital transformation hinges on a phased approach, careful planning, and effective employee training.
Mitigating potential risks and implementing a step-by-step guide is vital for a successful outcome. This approach ensures a controlled and sustainable integration of digital tools, avoiding overwhelming the existing infrastructure and workforce.
Phased Approach to Digital Transformation
A phased approach is essential for successful digital transformation in traditional manufacturing. It allows organizations to gradually integrate new technologies, manage the associated costs and complexity, and assess the impact of each stage before moving forward. This method enables a controlled rollout, minimizing disruptions and maximizing the return on investment.
Planning and Executing a Successful Digital Transformation Strategy
A comprehensive digital transformation strategy requires meticulous planning. This involves assessing current processes, identifying areas ripe for digitalization, and outlining a clear roadmap. This roadmap should include specific timelines, resource allocation, and key performance indicators (KPIs) for measuring progress. Furthermore, engaging with key stakeholders across departments is critical to garnering support and ensuring buy-in.
Employee Training Programs
Investing in comprehensive employee training programs is paramount for successful digital adoption. These programs should cover not only the technical aspects of new technologies but also the strategic implications and the impact on their daily work. Training should be tailored to specific roles and responsibilities, and should be delivered in a variety of formats to cater to different learning styles.
For example, interactive workshops, online modules, and on-the-job training can effectively equip employees with the necessary skills.
Examples of Effective Training Programs
Training programs can include hands-on workshops using simulation software to prepare employees for operating new equipment or software. Online learning platforms can provide accessible training materials, and mentorship programs can help employees develop practical skills and knowledge transfer. Successful companies have also utilized blended learning models, combining online resources with instructor-led sessions, to cater to diverse learning needs.
Managing and Mitigating Potential Risks
Potential risks during digital transformation include resistance to change, inadequate infrastructure, and security concerns. These risks need to be proactively addressed and mitigated. Establishing clear communication channels, fostering a culture of collaboration, and investing in robust security measures are essential steps in mitigating these challenges. Furthermore, contingency plans should be developed to address unforeseen issues and maintain business continuity.
Step-by-Step Guide for Implementing Digital Technologies
Implementing digital technologies in a traditional manufacturing setting requires a structured approach.
- Assessment and Planning: Analyze current processes and identify areas for digital improvement. Define clear objectives, timelines, and resource allocation. Establish a budget and prioritize the implementation of technologies based on their impact and feasibility.
- Technology Selection: Carefully evaluate various digital technologies, considering factors such as compatibility with existing infrastructure, scalability, and cost-effectiveness. Choose solutions that align with the organization’s strategic goals and specific needs.
- Implementation and Integration: Execute the selected technologies in a phased manner, ensuring seamless integration with existing systems. Implement robust data backup and recovery procedures.
- Training and Support: Equip employees with the necessary skills and knowledge to effectively utilize the new technologies. Provide ongoing support and resources to address any issues or questions.
- Monitoring and Evaluation: Track key performance indicators (KPIs) to measure the impact of the implemented technologies. Regularly review and adjust the strategy based on the gathered data and feedback from employees.
Closing Notes
In conclusion, Teknologi Digital Tantang Metode Manufaktur Tradisional underscores a crucial transition. Traditional methods are facing pressure from digital innovations, but they also offer a path toward greater efficiency, productivity, and adaptability. The future of manufacturing hinges on the ability to embrace these changes, fostering collaboration, and developing the necessary skills to navigate this digital age successfully.
Commonly Asked Questions: Teknologi Digital Tantang Metode Manufaktur Tradisional
What are the key limitations of traditional manufacturing methods?
Traditional methods often struggle with efficiency, cost control, quality consistency, and adapting to market demands. They can be inflexible and lack the real-time data analysis capabilities that digital tools offer.
How can companies effectively implement digital transformations?
A phased approach, careful planning, and employee training are crucial. Companies must identify specific areas for improvement, implement new technologies gradually, and ensure staff possess the necessary skills to operate and maintain the new systems.
What are some examples of specific digital technologies in manufacturing?
Automation, machine learning, AI, data analytics, 3D printing, and additive manufacturing are examples of digital technologies that can improve various aspects of traditional manufacturing, from production to decision-making.
What are the potential job role shifts in the digital manufacturing landscape?
The integration of digital technologies will likely lead to a shift in job roles, requiring workers to develop new skills in areas like data analysis, automation maintenance, and process optimization.