Minimalist Philosophy Transforms Production Methods by emphasizing efficiency and sustainability. This approach prioritizes resource optimization, waste reduction, and ethical sourcing throughout the entire production lifecycle. From material selection to supply chain management, minimalism reimagines traditional manufacturing processes, fostering a more streamlined and environmentally conscious approach.
The core tenets of minimalist philosophy, including the principles of mindful decision-making and waste elimination, are examined. This framework is contrasted with traditional approaches, highlighting the significant differences in resource allocation, product design, and manufacturing processes. Case studies and real-world examples illustrate the practical applications of minimalist production methods in various industries.
Defining Minimalist Philosophy
Minimalist philosophy, encompassing a wide range of approaches across various disciplines, emphasizes simplicity, efficiency, and the removal of unnecessary elements. It’s not merely about aesthetics, but a fundamental shift in perspective that values essentials and rejects superfluous details. This approach has profound implications for production methods, encouraging a focus on core functions and streamlined processes.
Core Tenets of Minimalist Philosophy
Minimalist philosophy prioritizes essential elements, reducing complexity and maximizing impact. This involves a critical evaluation of all aspects, from materials to processes, to identify and eliminate unnecessary steps or components. The focus is on functionality and effectiveness, not extravagance or superficiality. A key principle is the belief that less is often more, leading to greater clarity and efficiency.
Historical Context and Evolution
Minimalist thought has roots in various historical movements. From the artistic minimalism of the 20th century, which prioritized geometric forms and abstract expression, to the philosophical leanings of thinkers like Thoreau, who emphasized simplicity and self-sufficiency, the concept has evolved through time. Contemporary minimalist approaches often draw on these historical influences, adapting them to modern contexts. The evolution demonstrates a consistent human desire for streamlined approaches, from art to personal life, and now, to production.
Key Principles Guiding Minimalist Decision-Making
Minimalist decision-making is guided by a set of core principles. Prioritization of essential needs and functions is paramount. Evaluation of the true value of each element, be it a resource, process, or product feature, is crucial. Identifying and eliminating non-essential aspects is essential. This process fosters a streamlined approach, reducing waste and maximizing efficiency.
Ultimately, the focus is on the creation of optimal solutions.
Comparison with Other Philosophical Approaches to Production
Compared to traditional production methods, which often prioritize large-scale output and complex systems, minimalist approaches emphasize efficiency and reduced waste. Lean manufacturing, for example, shares some principles with minimalism, focusing on waste reduction. However, minimalist philosophy extends beyond the realm of cost-cutting to encompass a broader philosophical perspective, encompassing design, resource utilization, and product longevity.
Table: Traditional vs. Minimalist Production Approaches
Concept | Traditional Approach | Minimalist Approach | Explanation |
---|---|---|---|
Material Selection | Often driven by availability and cost, with little focus on sustainability or material longevity. | Prioritizes sustainable and ethically sourced materials, considering their entire lifecycle impact. | Minimalist production emphasizes using materials that are environmentally responsible and contribute to the long-term health of the planet. |
Process Optimization | Focuses on efficiency but often relies on complex and multi-step processes. | Strives for a streamlined, single-step or multi-step approach with fewer steps and higher efficiency. | The minimalist approach simplifies production methods to reduce errors, wasted time, and material usage. |
Waste Management | Waste is often treated as a byproduct and is managed through conventional methods. | Aims for zero waste by designing products and processes to eliminate waste generation at its source. | Minimalist production seeks to minimize the environmental impact of production by reducing the creation of waste altogether. |
Product Design | Often prioritizes features over function, resulting in complex and potentially unnecessary designs. | Emphasizes functionality, durability, and longevity over extraneous features. | Minimalist design centers around the essential features that meet the customer’s needs and ensures that the product will have a longer lifespan. |
Impact on Production Methods
Minimalist philosophy, when applied to production, fundamentally alters resource allocation and operational strategies. This shift prioritizes efficiency, reduces waste, and ultimately, streamlines the entire process. It compels manufacturers to reconsider their approach to materials, processes, and product design, ultimately aiming for greater sustainability and cost-effectiveness.
Resource Allocation in Manufacturing
A minimalist approach to manufacturing necessitates a rigorous assessment of resource allocation. Instead of maintaining excess inventory or over-provisioning for potential future needs, a minimalist strategy focuses on procuring precisely the required materials at the optimal time. This calculated approach minimizes storage costs, reduces the risk of obsolescence, and enhances the responsiveness of the production line to market demands.
The emphasis is on just-in-time delivery and production, ensuring that resources are only committed when absolutely necessary.
Waste Reduction in Minimalist Production
Waste reduction is integral to minimalist production. This isn’t just about eliminating physical waste like scrap materials; it encompasses a broader perspective. It includes minimizing time spent on non-value-added activities, reducing defects, and eliminating unnecessary steps in the production process. A lean approach is adopted to systematically identify and eliminate waste at every stage, from raw material acquisition to final product delivery.
This results in a more efficient and streamlined production process, ultimately reducing costs and improving profitability.
Impact on Product Design and Development
Minimalist production significantly impacts product design and development. Instead of creating complex products with numerous features, the focus shifts to essential functionality and streamlined designs. This emphasis on simplicity reduces production costs, simplifies manufacturing processes, and streamlines maintenance. Furthermore, simpler designs are often more aesthetically pleasing and appeal to a wider range of consumers. Products are meticulously crafted with a deep understanding of their intended purpose and the user experience.
Lean Manufacturing Principles in Minimalist Production
Lean manufacturing principles, emphasizing waste elimination and continuous improvement, align perfectly with the minimalist approach. By identifying and removing non-value-added activities, companies can optimize their production processes. This includes techniques like 5S (Sort, Set in Order, Shine, Standardize, Sustain), Kanban systems, and value stream mapping. The goal is to create a streamlined, efficient, and responsive production system capable of adapting to market demands.
Examples of Minimalist Production Strategies
Strategy | Description | Benefits | Challenges |
---|---|---|---|
Just-in-Time Inventory Management | Maintaining only the necessary inventory to meet immediate production needs. | Reduced storage costs, minimized risk of obsolescence, increased responsiveness to market demands. | Requires precise forecasting and reliable supplier relationships. Disruptions in supply chains can have significant impacts. |
Modular Design | Designing products with interchangeable modules, allowing for customization and easier maintenance. | Reduced production complexity, enhanced flexibility, and easier adaptability to changing market demands. | Requires careful planning and potentially higher initial design costs for the modular system. |
Value Stream Mapping | Visual representation of the entire production process, identifying areas for improvement and eliminating waste. | Enhanced visibility of the production process, pinpoint identification of inefficiencies, and increased overall production efficiency. | Requires a commitment to thorough data collection and analysis to implement changes effectively. |
Kaizen Events | Continuous improvement initiatives involving teams from different departments working collaboratively to solve production problems. | Empowers employees to identify and implement improvements, fostering a culture of continuous improvement. | Requires strong leadership and commitment from all levels of the organization to implement changes successfully. |
Material Selection and Procurement
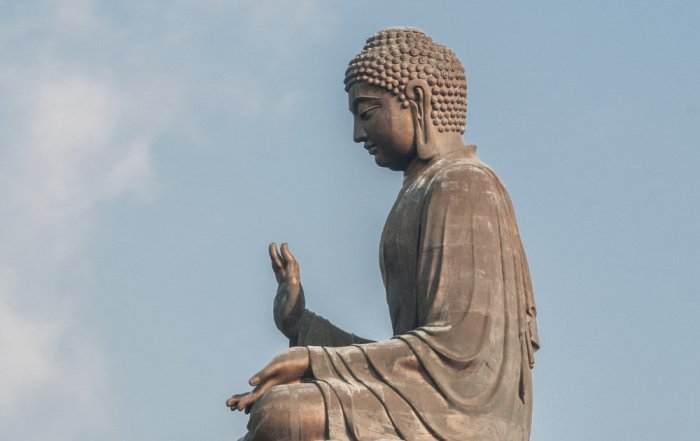
Source: thecorebasics.com
Minimalist philosophy, emphasizing functionality and lasting value, significantly impacts the material selection process for products. This approach prioritizes materials with inherent durability and sustainability, aiming to reduce environmental impact and promote ethical sourcing. Choosing materials wisely extends the product’s lifespan, aligns with the core principles of minimalism, and fosters a more responsible approach to consumption.Material selection in minimalist production extends beyond simply choosing a material.
It necessitates a careful evaluation of the material’s lifecycle, from extraction and processing to its eventual disposal. The goal is to minimize environmental harm at every stage, opting for materials that require less energy to produce and are readily recyclable or compostable. This commitment to sustainability is integral to the philosophy.
Influence of Minimalist Philosophy on Material Selection
Minimalist philosophy steers material selection towards durable, high-quality materials that stand the test of time. This preference for longevity contrasts with the often-exploited “fast fashion” model, where products are designed for disposability. By prioritizing durability, minimalist design aims to reduce the need for frequent replacements, thereby minimizing waste and environmental damage. This approach reduces the reliance on rapidly extracted resources, contributing to a more sustainable production process.
Examples of Sustainable and Ethically Sourced Materials
A variety of sustainable and ethically sourced materials are gaining prominence in minimalist production. These include recycled metals, organic cotton, reclaimed wood, and linen. Recycled materials, for example, significantly lessen the environmental impact of resource extraction. Furthermore, organic cotton production typically uses fewer pesticides and herbicides compared to conventional methods, promoting ethical labor practices. Other options, such as bamboo, offer fast growth cycles, reducing the strain on natural ecosystems.
Importance of Material Durability and Longevity
Minimalist design emphasizes the importance of material durability and longevity. Products designed with durability in mind tend to last longer, reducing the need for frequent replacements and minimizing waste. This focus on lasting value aligns perfectly with the minimalist principle of avoiding unnecessary consumption. By investing in materials that can withstand repeated use, minimalist products become more economical in the long run.
Impact of Material Waste Reduction on Production
Material waste reduction plays a crucial role in minimalist production. Minimizing waste throughout the production process, from raw material selection to manufacturing, significantly impacts the environmental footprint. Reducing material waste contributes to a more efficient and sustainable production process, and aligns with the principles of resource conservation. Furthermore, reducing waste can lead to cost savings in the long term.
Material Comparison Table
Material | Sustainability Rating | Durability | Cost |
---|---|---|---|
Recycled Steel | High | Very High | Medium |
Organic Cotton | Medium-High | Medium | Medium-High |
Reclaimed Wood | High | High | Medium-Low |
Bamboo | High | Medium | Low |
Manufacturing Processes and Tools
Minimalist philosophy, when applied to production, prioritizes efficiency and resource conservation. This extends beyond material selection to encompass the entire manufacturing process, emphasizing streamlined methods and reduced waste. This approach necessitates a critical examination of existing procedures and the implementation of innovative tools and techniques.A key aspect of minimalist production is the selection of manufacturing processes that minimize environmental impact and resource consumption.
This often translates to a preference for processes that are both efficient and precise, leading to a reduction in waste and rework. The use of automation and digital tools plays a pivotal role in achieving these goals.
Influence of Minimalist Philosophy on Manufacturing Processes
Minimalist philosophy promotes a systematic approach to manufacturing, focusing on eliminating non-essential steps and maximizing efficiency. This approach leads to the selection of manufacturing processes that prioritize speed, precision, and minimal waste generation. Examples include lean manufacturing techniques, which aim to eliminate waste in all its forms, and just-in-time inventory systems, which reduce warehousing costs and minimize material storage.
Automation and Digital Tools in Minimalist Production
Automation plays a significant role in minimalist production. Automated systems can perform repetitive tasks with precision and speed, minimizing human error and increasing overall output. Digital tools, such as computer-aided design (CAD) and computer-aided manufacturing (CAM) software, enable greater precision in the design and execution of manufacturing processes. This leads to higher quality products with fewer defects, further reducing waste.
For instance, automated assembly lines can ensure consistent product quality and reduce the time required to manufacture goods, aligning with minimalist principles.
Precision and Efficiency in Minimalist Manufacturing
Precision and efficiency are paramount in minimalist manufacturing. The use of high-precision machinery and tools ensures that products meet strict quality standards, minimizing the need for rework and reducing waste. This approach translates to reduced material consumption, lower energy use, and lower overall production costs. For example, laser cutting can achieve precise cuts with minimal material waste, aligning with the principles of minimizing resources and maximizing efficiency.
Minimizing Steps and Maximizing Efficiency
Minimalist manufacturing processes strive to minimize the number of steps involved in the production process. This reduces the potential for errors, delays, and waste. By streamlining workflows and eliminating redundant operations, companies can improve overall efficiency. This is exemplified by the 5S methodology, a workplace organization method that reduces waste and maximizes efficiency by organizing and maintaining the workspace.
Comparison of Manufacturing Techniques
Technique | Efficiency Rating | Waste Generation | Cost |
---|---|---|---|
CNC Machining | High | Low (with precision tools) | Medium-High |
Injection Molding | Medium-High | Medium (depending on design) | Medium |
3D Printing | Medium | Medium-High (material usage) | Variable, depending on material and complexity |
Traditional Machining | Low | High | Low |
Note: Efficiency ratings and cost are relative and can vary based on specific implementations and materials used.
Supply Chain Optimization
Minimalist philosophy, when applied to production, often necessitates a profound re-evaluation of the supply chain. This involves moving beyond simple cost reduction to a holistic approach that prioritizes transparency, ethical sourcing, and efficiency. A streamlined, responsive supply chain is integral to the success of minimalist production, ensuring that materials are sourced responsibly and products are delivered to consumers with minimal environmental impact.
Impact of Minimalist Philosophy on Supply Chain Management
Minimalist principles fundamentally shift the focus of supply chain management from solely cost-driven optimization to a more comprehensive approach. This entails a conscious effort to reduce waste throughout the entire process, from raw material acquisition to final product delivery. This often leads to closer relationships with suppliers, promoting shared responsibility for sustainability and ethical practices. Furthermore, a leaner supply chain with fewer intermediaries often results in quicker turnaround times and greater responsiveness to market demands.
Importance of Transparency and Ethical Sourcing
Transparency and ethical sourcing are paramount in minimalist supply chains. Consumers are increasingly aware of the environmental and social impact of their purchases, demanding greater visibility into the origin and production methods of goods. This necessitates clear communication throughout the supply chain, allowing consumers to understand the journey of their products. Ethical sourcing, in turn, ensures that materials are acquired responsibly, avoiding exploitation and supporting fair labor practices.
For example, companies using recycled or reclaimed materials can openly communicate the origin of these components to build consumer trust.
Impact of Shorter Supply Chains on Production Efficiency
Shorter supply chains often lead to increased production efficiency. By reducing the number of intermediaries, companies can gain greater control over production processes, enabling faster response times to changing market demands. This can translate to lower lead times, improved inventory management, and reduced waste. A reduced number of logistical steps also reduces the risk of delays and disruptions.
For instance, a company sourcing materials locally can react more swiftly to fluctuations in market prices.
Ways to Reduce Complexity and Waste in the Supply Chain, Minimalist Philosophy Transforms Production Methods
Minimizing complexity and waste in the supply chain is a critical aspect of minimalist production. This often involves streamlining processes, eliminating unnecessary steps, and optimizing inventory levels. For example, using digital platforms to manage inventory and track shipments can drastically reduce paperwork and improve communication flow. Reducing the number of suppliers to a smaller group of reliable partners, or consolidating logistics providers, are further examples of optimizing the supply chain.
Measures to Reduce Lead Times and Increase Responsiveness
Reduced lead times and increased responsiveness are crucial for effective minimalist supply chains. Implementing agile manufacturing techniques, coupled with close collaboration with suppliers, enables faster production cycles. Utilizing real-time data analytics to monitor supply chain performance and identify potential bottlenecks is also essential. Implementing just-in-time inventory management systems can reduce storage costs and enhance responsiveness to market fluctuations.
Benefits of Optimizing the Supply Chain
Optimization Method | Description | Impact on Production | Cost Savings |
---|---|---|---|
Reduced Intermediaries | Streamlining the supply chain by eliminating unnecessary middlemen. | Faster delivery times, improved communication, reduced lead times. | Lower transportation costs, reduced administrative overhead. |
Ethical Sourcing | Prioritizing suppliers who adhere to fair labor practices and environmental standards. | Improved brand reputation, enhanced consumer trust, reduced risks of reputational damage. | Reduced legal and reputational risks, potentially higher employee retention rates. |
Just-in-Time Inventory | Holding only the necessary materials for immediate production. | Reduced storage costs, decreased inventory obsolescence, increased agility. | Lower storage costs, reduced capital tied up in inventory. |
Data-Driven Analysis | Utilizing real-time data to track and analyze supply chain performance. | Improved forecasting accuracy, identification of bottlenecks, and proactive problem-solving. | Reduced waste and delays, improved efficiency leading to lower overall costs. |
Product Life Cycle Management
Minimalist philosophy emphasizes the entire lifecycle of a product, moving beyond simply designing and producing it. This approach considers the environmental and social impact from raw material extraction to end-of-life disposal. A key tenet is to design for durability and repairability, extending product lifespan and minimizing waste.Product longevity and ease of repair are not mere design considerations but fundamental principles.
By anticipating the potential for reuse and recycling, minimalist design minimizes the strain on resources and reduces the environmental footprint of consumption. This extends to the selection of materials, manufacturing processes, and the overall product lifecycle.
Product Durability and Repairability
Minimalist design prioritizes durability to extend a product’s useful life. This extends beyond simply creating a product that lasts longer; it involves designing for ease of repair and reuse. Components are chosen for their repairability and longevity, ensuring the product can be maintained and upgraded rather than being discarded. This is particularly important in minimizing waste.
Product Lifespan Extension and Circularity
A central concept in minimalist production is extending the product’s lifespan through design for durability, repairability, and potential reuse. This promotes a circular economy, where materials are kept in use for as long as possible, minimizing the need for new resource extraction. This contrasts sharply with the linear “take-make-dispose” model, which is unsustainable. Examples include designing products with modular components allowing for upgrades and repairs, or creating products with a specific end-of-life plan for disassembly and material recovery.
Designing for Ease of Repair and Reuse
Designing for repair and reuse involves careful consideration of component design, material selection, and assembly methods. Modular designs allow for easier component replacement and upgrades. Using standardized parts and interfaces facilitates repair by authorized technicians and consumers. Documentation and repair guides are crucial, ensuring accessibility to information needed for maintenance and repair.
Measures to Encourage Product Reuse and Recycling
Incentivizing reuse and recycling necessitates a multifaceted approach. Design for disassembly and material separation simplifies recycling processes, allowing for the recovery of valuable materials. Clear labeling and material identification are essential to enable effective sorting and processing during recycling. Education and awareness campaigns are crucial to encourage consumers to participate in these initiatives. Additionally, creating repair networks and supporting local repair services can extend product life and decrease waste.
Designing Products for Durability and Longevity
Step | Description | Materials Used | Cost |
---|---|---|---|
1. Material Selection | Choose durable and repairable materials with a focus on recyclability and minimal environmental impact. | Recycled steel, renewable polymers, or natural fibers | Potentially higher upfront cost, but lower long-term cost due to reduced replacement needs. |
2. Component Design | Design components for easy disassembly and repair, using standardized interfaces and modularity. | Standardized fasteners, easily accessible components. | Slight increase in initial design time and potentially tooling costs. |
3. Manufacturing Process Optimization | Implement manufacturing processes that minimize waste and maximize material efficiency. | Optimized cutting, welding, or assembly methods. | Potential for slightly higher initial investment in specialized equipment. |
4. End-of-Life Planning | Anticipate the end of the product’s life and plan for its disassembly, reuse, or recycling. | Clear labeling for disassembly, identification of recyclable materials. | Potential for minor cost increase due to planning and documentation. |
Illustrative Examples of Minimalist Production
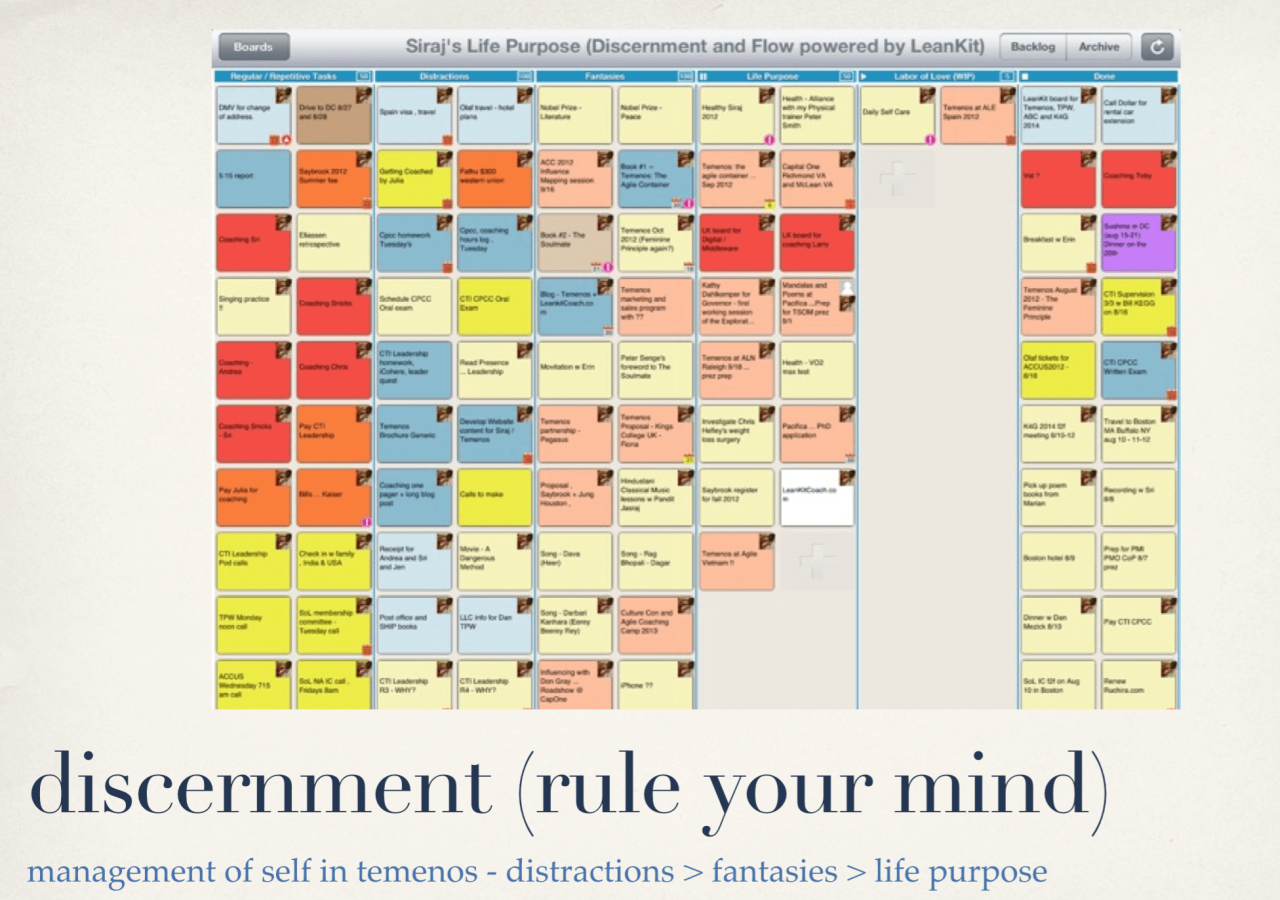
Source: visiontemenos.com
Minimalist production methods, when effectively implemented, can yield significant benefits across various industries. These approaches, focused on streamlining processes and reducing waste, often lead to improved efficiency, lower costs, and increased profitability. This section explores real-world examples of companies successfully embracing minimalist principles.Companies adopting minimalist production principles frequently see a reduction in operational complexity and an increase in overall efficiency.
This simplified approach allows them to allocate resources more strategically, fostering innovation and enabling quicker responses to market demands.
Examples of Companies Implementing Minimalist Production
Numerous companies have successfully integrated minimalist principles into their operations. These companies, across diverse sectors, have demonstrated the viability and benefits of this approach.
- Ikea: Known for its flat-pack furniture, Ikea exemplifies minimalist design and production. Their emphasis on modularity and standardized components reduces material waste and complexity in the manufacturing process. This streamlined approach allows for efficient assembly and transport, contributing to lower costs and faster turnaround times. Furthermore, the standardized designs facilitate mass production while minimizing variation and maximizing efficiency.
- Tesla: Tesla’s production model showcases a minimalist approach to automotive manufacturing. Their focus on vertical integration, automation, and a streamlined supply chain has significantly reduced production costs and lead times. The elimination of unnecessary parts and features, along with the use of readily available and sustainable materials, further exemplifies the minimalist principles.
- Apple: Apple’s minimalist design aesthetic is well-known. Their focus on sleek, functional products, often using a limited palette of materials, aligns with minimalist principles. The company’s emphasis on simplicity in design translates to a streamlined manufacturing process, minimizing waste and maximizing efficiency. Moreover, Apple’s focus on quality control ensures that the final product aligns with their strict design standards.
Application of Minimalist Principles in Different Industries
Minimalist principles can be applied across various industries, leading to positive outcomes in each. The following examples highlight the versatility of these principles.
- Electronics: Companies like Apple and Samsung have used minimalist design principles in their electronics products, focusing on a sleek form factor and essential functionality. The reduction of unnecessary features and components has resulted in more efficient manufacturing processes and a reduced environmental impact. The design focus on less is more, often with high-quality materials, has created a desirable aesthetic for consumers.
- Fashion: Brands focusing on sustainable practices and ethical production often incorporate minimalist principles. This includes using less material, streamlining design processes, and focusing on durability over trends. This approach often appeals to environmentally conscious consumers and contributes to a more sustainable fashion industry. The minimalist focus on quality over quantity often yields more satisfied customers.
- Food and Beverage: In the food industry, minimalism translates to focusing on the core ingredients and preparation methods. This can result in less processing and fewer additives, leading to healthier and more natural products. The elimination of unnecessary ingredients and packaging contributes to a more sustainable and consumer-friendly product.
Case Studies and Examples of Minimalist Production
“A key element of minimalist production is the elimination of unnecessary complexity and waste in every stage of the production process.”
Product | Design Features | Material | Production Method |
---|---|---|---|
Minimalist Laptop | Sleek, lightweight, high-performance | Recycled Aluminum, Carbon Fiber | Automated Assembly Lines |
Simple T-Shirt | Durable, comfortable, classic design | Organic Cotton | Optimized Sewing Processes |
Sustainable Smartphone Case | Minimalist aesthetic, robust protection | Recycled Plastic | 3D Printing with Optimized Materials |
Final Thoughts
In conclusion, Minimalist Philosophy Transforms Production Methods by driving significant improvements in efficiency, sustainability, and ethical considerations. By minimizing waste, optimizing resource allocation, and prioritizing product longevity, this approach fosters a more environmentally friendly and economically viable manufacturing process. The exploration of minimalist principles reveals a path toward a more sustainable future for production and consumption.
FAQs: Minimalist Philosophy Transforms Production Methods
What are the key differences between traditional and minimalist production approaches?
Traditional production often prioritizes maximizing output and minimizing initial costs, sometimes at the expense of long-term sustainability and ethical considerations. Minimalist production, conversely, emphasizes resource optimization, waste reduction, and ethical sourcing throughout the entire lifecycle of a product.
How does minimalist philosophy influence material selection?
Minimalist philosophy emphasizes the selection of durable, sustainable, and ethically sourced materials. This consideration extends beyond the initial cost to include environmental impact and the long-term lifespan of the product.
What role does automation play in minimalist production?
Automation is often a key component of minimalist production. By streamlining processes and eliminating unnecessary steps, automation contributes to efficiency and reduces waste.
What are some common challenges associated with implementing minimalist production methods?
Implementing minimalist production methods can present challenges, including initial investment costs for new technologies and potentially higher material costs for sustainable alternatives. However, the long-term benefits often outweigh these initial hurdles.